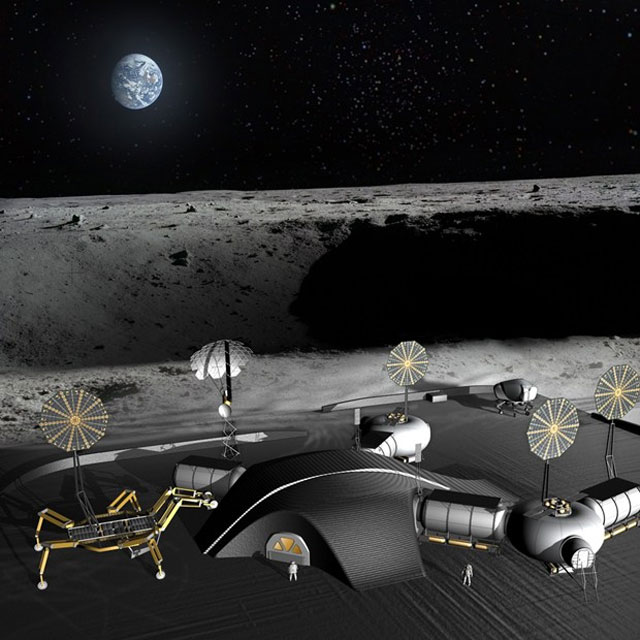
The first lunar base on the Moon may not be built by human hands, but rather by a giant spider-like robot built by NASA that can bind the dusty soil into giant bubble structures where astronauts can live, conduct experiments, relax or perhaps even cultivate crops.
We've already covered the European Space Agency's (ESA) work with architecture firm Foster + Partners on a proposal for a 3D-printed moonbase, and there are similarities between the two bases—both would be located in Shackleton Crater near the Moon's south pole, where sunlight (and thus solar energy) is nearly constant due to the Moon's inclination on the crater's rim, and both use lunar dust as their basic building material. However, while the ESA's building would be constructed almost exactly the same way a house would be 3D-printed on Earth, this latest wheeze—SinterHab—uses NASA technology for something a fair bit more ambitious.
The product of joint research first started between space architects Tomas Rousek, Katarina Eriksson and Ondrej Doule and scientists from NASA's Jet Propulsion Laboratory (JPL), SinterHab is so-named because it involves sintering lunar dust—that is, heating it up to just below its melting point, where the fine nanoparticle powders fuse and become one solid block a bit like a piece of ceramic. To do this, the JPL engineers propose using microwaves no more powerful than those found in a kitchen unit, with tiny particles easily reaching between 1200 and 1500 degrees Celsius.
Nanoparticles of iron within lunar soil are heated at certain microwave frequencies, enabling efficient heating and binding of the dust to itself. Not having to fly binding agent from Earth along with a 3D printer is a major advantage over the ESA/Foster + Partners plan. The solar panels to power the microwaves would, like the moon base itself, be based near or on the rim of Shackleton Crater in near-perpetual sunlight.
"Bubbles" of binded dust could be built by a huge six-legged robot (OK, so it's not technically a spider) that can then be assembled into habitats large enough for astronauts to use as a base. This "Sinterator system" would use the JPL's Athlete rover, a half-scale prototype of which has already been built and tested. It's a human-controlled robotic space rover with wheels at the end of its 8.2m limbs and a detachable habitable capsule mounted at the top.
Here's a video of it dancing, because science:
ATHLETE Rover Busts a Move: A Dancing Robot
Athlete's arms have several different functions, dependent on what it needs to do at any point. It has 48 3D cameras that stream video to its operator either inside the capsule, elsewhere on the Moon or back on Earth, it's got a payload capacity of 300kg in Earth gravity, and it can scoop, dig, grab at and generally poke around in the soil fairly easily, giving it the combined abilities of a normal rover and a construction vehicle. It can even split into two smaller three-legged rovers at any time if needed. In the Sinterator system, a microwave 3D printer would be mounted on one of the Athlete's legs and used to build the base.
Rousek explained the background of the idea to Wired.co.uk: "Since many of my buildings have advanced geometry that you can't cut easily from sheet material, I started using 3D printing for rapid prototyping of my architecture models. The construction industry is still lagging several decades behind car and electronics production. The buildings now are terribly wasteful and imprecise—I have always dreamed about creating a factory where the buildings would be robotically mass-produced with parametric personalization, using composite materials and 3D printing. It would be also great to use local materials and precise manufacturing on-site."
He continued: "It's good to realize that we have this unique chance to jump from our atmosphere and go to the next evolutionary level—it's comparable with leaving the ocean and climbing down from the trees. I went to Strasbourg to study space architecture at the International Space University in France, where I formed the team with Ondrej Doule and Katarina Eriksson. Our friend there, Richard Rieber from NASA's JPL, is one of the co-authors of the 3D printing system based on the Athlete robot. We were inspired by their invention and immediately started designing architecture that would use this technology."
Sintering is quite cheap, in terms of power as well as materials, and an Athlete rover should be able to construct a bubble volume in only two weeks, Rousek estimates. He said: "It would have a very good cost-value ratio as you don't need to import as much material from Earth. The whole expandable module, with the membranes to cover the base when built, would be carried by the same rocket that would bring other modules of the outpost, but it can build a volume four times bigger than a rigid cylindrical module. Since we don't have the necessary transport capacity to the Moon at the moment, estimating a price now would be very inaccurate. As a comparison, the International Space Station has so far cost approximately $150bn (£99bn) but a lunar base could be designed much more cheaply with private companies."
Another benefit of sintering is that astronauts could use it on the surface of the Moon surrounding their base, binding dust and stopping it from clogging their equipment. Moon dust is extremely abrasive -- without natural weathering or erosion like on Earth, dust isn't ground down into smooth spheres. Instead it remains tiny yet jagged, perfect for getting into any exposed cracks, scratching lenses, wearing down airtight seals and becoming deeply embedded into human lungs. Former Apollo astronaut Harrison Schmidt has called the dust the biggest environmental issue on the Moon, even more so than radiation (which in SinterHab would be blocked by a combination of the Moon dust structure, "strategically located water tanks" and layers of inflatable polymers).
London-based space architect Rousek, director of A-ETC, has continued working on SinterHab with Doule and Eriksson since first proposing the idea in 2010 at the International Aeronautical Congress as a way of taking advantage of the Sinterator system. The design—now published in the journal Acta Astronautica—is based on the equilibrium found in bubbles. You might have noticed, the last time that you had a bubble bath, the way that groups of bubbles join together naturally to form a more solid structure -- that's exactly what SinterHab will look like. A bunch of rocky bubbles connected together, with cladding added later. Rousek explained: "The internal structure was selected to demonstrate how we can arrange the interior and create walls inside. The first version should probably have only a single volume to decrease the risk. Then we could think about a bigger module, which would use connected volumes."
A second version of SinterHab—SinterHab 2.0—is "currently being developed under the leadership of Ondrej Doule from the Florida Institute of Technology," Rousek said. "We plan to further develop the interior design, deployment and construction process and life-support system. We would like to also do research about possible spin-offs of such construction methods on Earth."
NASA is keen on figuring out a way to build a lunar base, and as one of several proposals being batted around inside the organization it's been used in a proposal for further development of sintering technology—and I, for one, welcome our new robo-spider space architect overlords.
No comments:
Post a Comment
Let us know your Thoughts and ideas!
Your comment will be deleted if you
Spam , Adv. Or use of bad language!
Try not to! And thank for visiting and for the comment
Keep visiting and spread and share our post !!
Sharing is a kind way of caring!! Thanks again!