
A Ford Taurus SHO Ecoboost engine, neatly disassembled and spread across the floor.
Despite this system’s longevity, we’re still finding ways to make engines more efficient. Like any machine, internal combustion engines waste a lot of their theoretical performance—less than 30 percent of the energy in each drop of gas is used to actually move the car. That's because engines are complicated machines with lots of moving pieces of metal, and moving them around thousands of times a minute generates waste heat. Sucking air into a cylinder at a lower engine speed is also harder than doing it at 6000 rpm. Accessories like the water pump and alternator all suck away some power, too.Suck. Squeeze. Bang. Blow. There’s no joke to be made there—you’re looking at the DNA of the four-stroke internal combustion engine, virtually unchanged since Dr. Nikolaus Otto first built it in Germany back in 1876.
Careful design work on these bits won't double power or efficiency, but lots of small improvements here and there add up. More significant gains can most easily be achieved by getting more air into the cylinder, so it's here that many of the world's largest car makers have focused their R&D efforts, taking advantage of the breathtaking increase in computing power to build engines that would be unthinkable even a couple of decades ago. The tech has already begun to pay real dividends to drivers. Here's how it works.
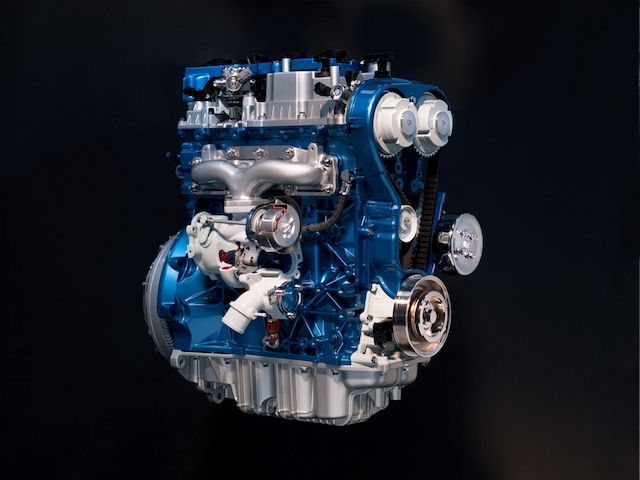
Ford's 1.6 L four-cylinder EcoBoost engine.
Take it from the top
As the name suggests, the internal combustion engine—unlike a steam engine—burns its fuel inside the engine housing. The process has four basic stages. It starts with a combustion chamber capped at one end by intake and exhaust valves, then by a piston, connected to a crankshaft, at the other. As the crankshaft turns, the piston drops to the bottom of the cylinder, sucking in air from the intake valve (this is called the "intake stroke"). At the same time, fuel is sprayed in to the expanding cylinder, which mixes with the air. As the crankshaft continues to rotate, the piston moves back up and compresses this fuel and air mix (the "compression stroke"). Once the piston is at the top of the cylinder and the fuel-air mix is under the greatest pressure, it's ignited by a spark. This causes it to explode, which in turn pushes the piston back down again, turning the crankshaft ("the power stroke"). Finally, as the piston moves back up once more, the exhaust valves open and exit, stage right ("the exhaust stroke").
The flow of air into the engine is controlled by a throttle valve, sitting between the air intake and the engine manifold. Pushing on the right-most pedal in your car opens this valve further. Sensors measure the amount of air coming in, as well as how hot it is. Based on this information, the engine knows how much fuel to add and the spark plugs know when to fire. More air means more fuel, which together mean larger explosions. Larger explosions have more energy to transfer to the pistons, which turn the crankshaft more rapidly.
In a conventional engine, the intake and exhaust valves are controlled by a camshaft, which is turned by the crankshaft (which in turn rotates as the pistons force it down during each bang). Lobes on the cam push each valve open and then allow it to close, timed for each stroke of the cycle. The timing of valves opening and closing is fixed by the shape of the lobes on the camshaft. The amount the valve opens is fixed, too (this is called valve lift). The simplest engines have one intake and one exhaust valve per cylinder, both controlled by a single camshaft. By using two camshafts—one for intake valves and one for exhaust valves—each cylinder can have two or even three intake valves and two exhaust valves, making it easier to get air into and out of the engine. The aim is to get as much air as possible, sometimes expressed as volumetric efficiency. For instance: a two liter engine that sucks in two liters of air each cycle would have a volumetric efficiency of 100 percent. In practice, most engines have a much lower figure.
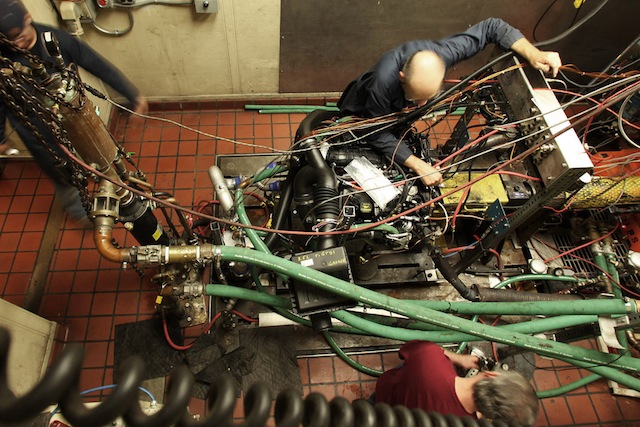
The Ford F-150 EcoBoost engine being put through a torture test.
Car engines have to operate under lots of different conditions—at idle, under partial load, at full throttle—and we expect them to perform well, no matter what. Engineers have to design the engine to perform well in each scenario, but this comes at the cost of being optimal at none. Building a fixed timing engine that idles well gives up some top end performance; getting good top end performance means giving up some fuel efficiency at lower revs (not to mention more emissions).
When the throttle is fully open at high revs, the goal is to produce as much power as possible. To maximize the amount of air in the cylinder, the intake valves should be open as long as possible even before the start of the intake stroke, then remain open into the compression stroke. Opening the valve before the intake stroke allows it to begin filling the cylinder even as it starts increasing in volume. And, as the mass of air is pulled in by the partial vacuum, it gains momentum that doesn't disappear instantly just because the next stroke has started or because a valve is trying to close against it.
Similarly, it's a good idea to open the exhaust valves a little before the exhaust stroke starts. It requires effort to move the piston up during the exhaust stroke, and opening the exhaust valve a little before the start of the exhaust stroke reduces the pressure the piston has to work against. Ultimately, this decreases frictional losses in the engine. And, as with the air coming into the engine during intake, the exhaust gases have momentum that won't disappear when the piston begins its next stroke (so the exhaust valves can be open for part of the intake stroke).
As a result, engines have an overlap period when both intake and exhaust valves are open. For high performance, a longer overlap is beneficial, but at low engine speed the pistons aren't moving as quickly, the partial vacuum generated by the expanding cylinder volume is lower, and so the velocity of the air being sucked into the cylinder is lower. At low engine speed, that means a long overlap can allow exhaust gases to enter the manifold and unburned fuel to exit the exhaust valves. This is why highly tuned engines like those in race cars don't like idling very much.
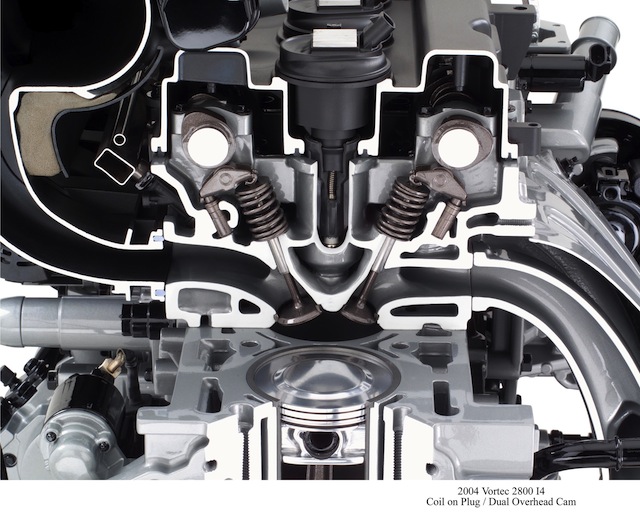
A cutaway of an engine showing the intake (left) and exhaust (right) valves.
Variety: the spice of (engine) life
Recall that different engine speeds and loads demand different timing of the intake and exhaust valves. So varying the valve timing (when it opens in the cycle), valve lift, and duration with different lobe profiles can provide a solution to increasing engine efficiency across the rev range. Honda's VTEC (Variable Valve Timing and Electronic Lift Control) is probably the best known such system, thanks to a legion of Internet memes. But many car manufacturers have variable valve timing systems using a number of different approaches.
Engines with a single camshaft may only be able to vary either intake or exhaust valves, but engines with double camshafts can have variable timing on both. In a simple variable valve timing system, the camshaft will have two lobes that control the opening of its valves: one optimized for low speed, and a second that opens the valve earlier, closes it later, or opens it more. When a certain engine speed has been reached (4000 rpm, for example) the engine will switch from using one set of lobes to another (this is where you can feel the VTEC kicking in, yo).
The simplest variable valve timing systems were only optimized for two conditions. In recent years, plenty of work has gone into developing continuously variable valve timing systems that can judge how and when to alter both intake and exhaust valve opening plus lift based on variables such as oil temperature or vehicle speed. BMW was first to market with its Valvetronic system that changed the amount of intake valve lift and duration according to how much the accelerator pedal is pressed.
In a conventional engine, the more you press the accelerator pedal, the more the throttle valve opens. With Valvetronic, the accelerator pedal controls valve lift instead, opening the valves wider and longer. That allows more air into the cylinders when more power is called for, increasing efficiency by around ten percent.
Even more can be gained when both the intake and exhaust valves can be altered, opening the valves earlier or later, closing them earlier or later, and opening them for longer or shorter periods. In BMW's case, that has been done with a system called VANOS. It changes the position of the camshafts relative to the crankshaft. At low and high engine speeds, the intake valve timing is delayed, opening later in the cycle. But in the middle of the rev range, the intake valves open earlier in the cycle to increase fuel-air mixing, boosting efficiency and decreasing emissions.
Going mainstream
So far, all of the methods employed—from VTEC to VANOS to VVT-i on through an entire dictionary of acronyms beginning with the letter V—have been mechanical systems which add complexity and cost to engines. This is less of a problem if you're BMW or Porsche and customers expect you to charge them a lot for an engine. But in the higher volume side of the market, where margins are already low, mechanical variable valve timing is often considered impractical.
Enter Fiat's hydraulic MultiAir technology, which moves variable valve timing into the digital realm. Like Valvetronic, the flow of air into a MultiAir engine is controlled by intake valves and not a throttle valve. The engine has one camshaft that's turned by the crankshaft as usual, and the exhaust valves work the same as in any other engine. The intake valves, however, have a pair of hydraulic dampers between them and the camshaft. Unlike a simple, shaped piece of metal (a normal camshaft), hydraulic dampers can be controlled electronically and accurately, varying the force that's transmitted to the valves. Fiat has worked out how to use the dampers to change valve timing as well as to control valve lift.
The camshaft profile is optimized for better performance at maximum load. When this is called for, the hydraulics transmit all of the force from the camshaft to the valves, whereupon they open fully, burning the gas in the highest volume of air. But engines with aggressive camshafts that are good under load can be temperamental starting from cold or idling below 2000 rpm. They suffer from backflow of air into the manifold from the cylinder under partial load, and more of their time will be spent there than pinging off the rev limiter. Ordinarily that would mean horrible fuel economy and lots of noxious exhaust products.
MultiAir compensates for these problems with a number of different modes, and each cylinder is controlled independently and adapts on the fly. When the engine is started, or when it's idling, there's no point producing full power. Any fuel you'd use to do so would be wasted, rather than being used to get you from A to B. Under these conditions, MultiAir opens the intake valves later in the intake cycle. As open cylinder space is already increasing in volume (because the piston is moving down), the air flows in through the valves at a higher velocity and mixes better with the fuel injected, with the added benefit of fewer unwanted combustion products.
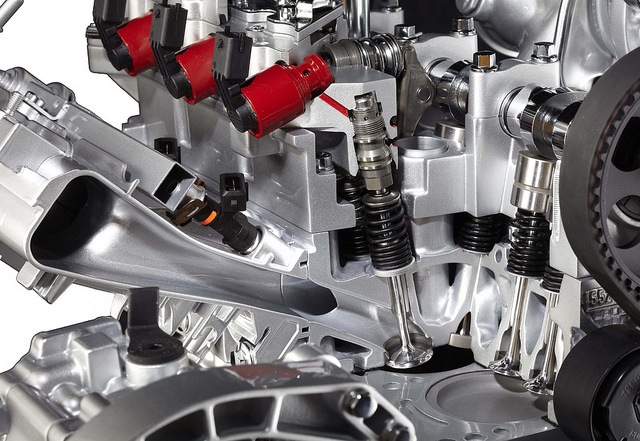
A cutaway of a Fiat 500 Abarth's 1.4-liter MultiAir Turbo engine. The intake valves are to the left, below the red MultiAir hydraulic reservoir
Conversely, the intake valves close early under partial load. This cuts down on the backflow of air into the manifold from the cylinder. For stop/start traffic—the natural home of both the Fiat 500 and the average American commuter—the intake valves can be opened and closed twice during a single intake stroke.
Fiat claims that MultiAir has given them ten percent more power and 15 percent more torque, as well as cutting fuel consumption by ten percent. And if that isn’t enough, some very impressive figures claim up to a 40 percent reduction in exhaust hydrocarbons and carbon monoxide, plus a 60 percent reduction in nitrogen oxides. Small capacity (1.4 L) MultiAir engines are already on our roads in the Fiat 500, but Fiat's control of Chrysler—and the modular nature of MultiAir—means that we'll see it in larger cars and on larger engines before too long. At some point Fiat will begin to license the technology to others as well.
Turbo gets tiny
Yet another approach to efficiency involves keeping the intake and exhaust valves closed entirely for individual cylinders, reducing the displacement of the engine when under light loads (such as cruising on the freeway). V8 engines, because of the way they're balanced, lend themselves best to this technique, although Honda has been using variable displacement in V6 engines, too. GM's newer pushrod V8s use solenoids to deactivate the lifters to half of the cylinders. (A pushrod engine has the camshaft between the two banks of cylinders in the middle of the V, connected to the valves by, yes, pushrods). "Rather than adding turbochargers or multi-valve cylinder heads to increase the power of smaller engines, we chose to keep the proven capability of our larger V8 truck engines, and save fuel by switching off half of the cylinders when they aren’t needed," said Jordan Lee, GM's global chief engineer for Small Block Engines, in a recent company press release.
The ten percent efficiency gain brought about by MultiAir is worth maybe double the efficiency gain of more conventional mechanical variable valve timing systems. But there's an easier way to get more air into each cylinder: forced induction. All of the engines described previously rely on the difference between atmospheric pressure and the lower pressure inside the expanding cylinder to suck air inside. This is known as normal aspiration. The very best normally aspirated engines might have a volumetric efficiency of 110 percent by using cleverly shaped intake manifolds that increase the pressure of the incoming air above that of the outside world. By contrast, forced induction engines can have volumetric efficiencies of 150 percent or more—in plain English, that means a turbocharged 1.4 L engine can put out as much power as a normally aspirated engine of 2.5 L even though it's smaller and uses less fuel.
Forcing air into the cylinders with a pump dates back to the nineteenth century. Before World War II, this was most commonly done with a supercharger, where the air compressor is powered by a belt (or a chain or gears) driven by the engine's crankshaft. This comes at the expense of more mechanical complexity (those belts, gears, pulleys, or chains are yet another thing that could break) and an increase in parasitic load. A supercharger might add 40 hp, but at the same time will require 15 hp from the engine to work.
Turbocharging does away with the complexity of belts, gears, pulleys, and the like, instead using the exhaust gases that would otherwise just head out the tail pipe. The vehicle's exhaust is routed so the flow of gases rotates a turbine, which drives an impeller pump to suck in air and compress it on its way into the cylinders. This is essentially recovering free energy. There's no parasitic drain on the engine to run the turbocharger, but it does require enough exhaust gas to spin the turbine. If the engine isn't running fast enough, the turbo won't provide any extra power and there will always be a slight delay ("turbo lag") between giving it some beans and disappearing off toward the horizon.
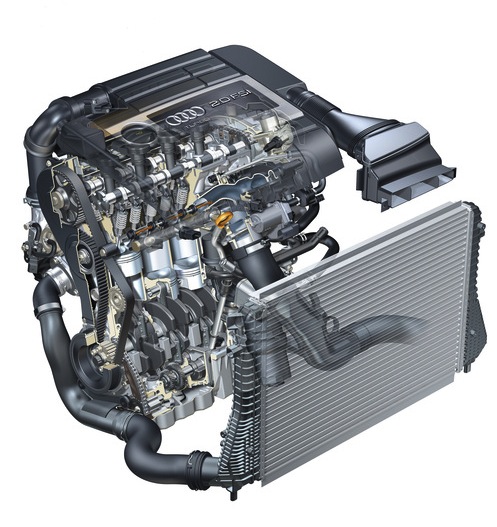
A cutaway of Audi's TFSI engine. Clever stuff.
Back in the olden days of the 1980s, when turbocharging was the in thing (even PCs came with turbo buttons), turbos usually meant lots of top end power coupled with horrendous lag. But as car manufacturers are trying to square competing demands—increasing fleet efficiency, decreasing pollutants, maintaining happy customers used to larger capacity engines—the small capacity turbo is rapidly getting set to replace those bigger, thirstier V6s and V8s. When coupled with variable valve timing or direct injection of fuel (more on this a little later) and the use of advanced materials, the result is a 1.4 L turbo engine in a midsize car that makes more power and the same mileage as a 2 L naturally aspirated one. It can produce a crossover SUV with a 1.6 L turbo engine that beats the normally aspirated 2.5 L version without even breaking a sweat.
Take Ford, for example. The blue oval has a fair bit of experience with turbocharged cars, mainly for use in racing. Now, Ford is applying the lessons it learned in search of performance to bring about fuel economy for the masses with EcoBoost engines. I spoke to Dan Kapp, Ford's director of Powertrain Research and Advanced Engineering, who argues that advanced turbo engines are a lower cost strategy compared to building hybrids and better for carmakers who want to sell in volume. (Ford will have sold over a million EcoBoost-powered cars by 2013.)
Kapp has been pleasantly surprised by his customers' reactions to the new EcoBoost engines, especially in Ford trucks (traditionally the province of a large, lazy V8). In the F-150 pickup truck, the 3.5 L EcoBoost engine gets the same gas mileage as the normally aspirated 3.7 L V6 but delivers more power than the 5 L V8 and more torque than the 6.2 L V8 engines. Truck buyers have evidently also been impressed, with 40 percent of them opting for the blown engine. After spending some time with a new Ford Escape, I can report that the 1.6 L EcoBoost did an exemplary job of shifting the vehicle's 3,500 lbs during my 10 mile commute through Washington, DC and Bethesda, Maryland. Even 30 mpg is possible on the highway.
Ford is not exactly going out on a limb with this approach. Although the Volt might be generating most of the headlines, General Motors also sees small turbo engines as the way forward, at least when it comes to highway driving. GM Engineering Group Manager for Charging Rick Balsley told me that it was all about tailoring the technology to the customer and their usage. It was something I heard repeatedly from everyone I spoke to for this piece: it doesn't matter how clever the tech is if customers aren't interested.
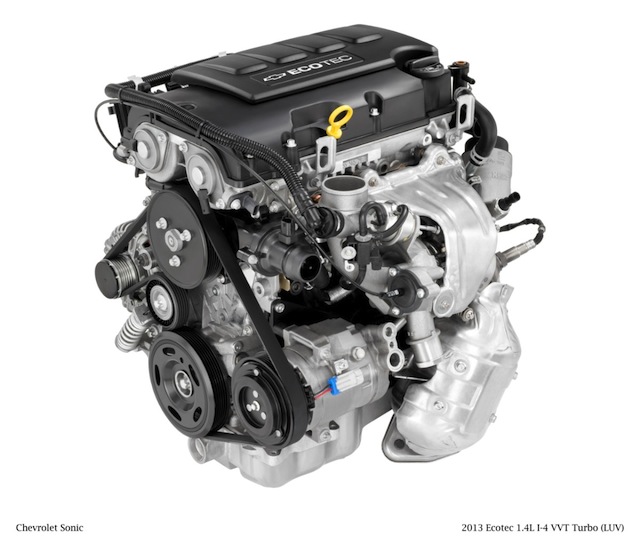
Chevrolet's 1.4 L Ecotec Turbo
When it comes to designing these new engines, GM's powertrain engineers are looking for low end torque and transient response, not for huge horsepower. According to Balsley, customers expect familiarity in the way cars drive and sound. This has moved the turbo away from the being something you'd take racing to an everyday part, but this means it has to be able to cope with everyday neglect. Those of you who remember earlier turbocharged cars might recall having to leave the engine running for a few minutes after a particularly hard drive—vital to prevent heat soak from damaging the turbo. Now, carmakers use water-cooled bearing housings, meaning you can turn the key and walk away without fear. Modern electronics are now able to control wastegates (valves that divert exhaust gases away from the turbine) to ensure optimum boost pressure. And materials science has also had a role. Turbos have to last as long as the rest of the engine; that means 100,000 miles, spinning at 220,000 rpm at 950˚C. I was surprised to find that GM rejected ceramic turbine blades in favor of superalloys for just this reason.
Knock, knock
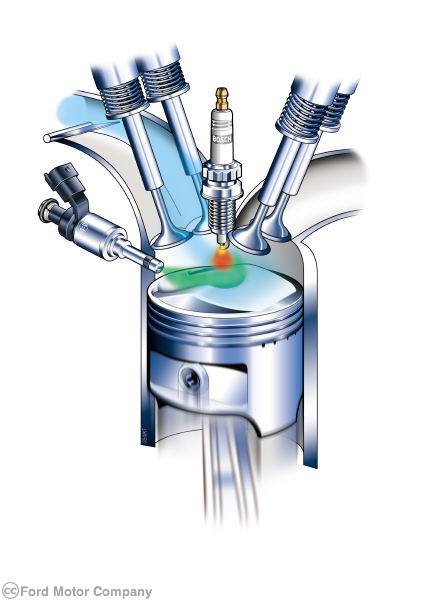
With EcoBoost's direct injection, fuel is injected into each cylinder of an engine in small precise amounts. Compared to conventional port injection, direct injection produces a cooler and denser charge, delivering higher fuel economy and performance.
Ford's EcoBoost engines combine turbochargers with direct injection of fuel into the cylinders, something Audi has pioneered after perfecting the system on their Le Mans-winning R8 race cars in the early 2000s. Until the introduction of direct injection, fuel was added to the incoming air a little upstream of the intake valves. Direct injection uses a much higher pressure system (up to 3000 PSI vs. 100 PSI for normal fuel injection) and sprays the fuel into each cylinder during the compression stroke. Direct injection makes for a better fuel-air mixture inside the cylinder, but it has some other benefits as well, especially with turbocharged engines. If the air and fuel mixture gets too hot, it can prematurely detonate (knock) in the cylinder during the compression stroke and before the spark plugs fire. Preventing this knocking is why additives like lead (and more recently MTBE) are added to gas.
Because knock is a function of heat and pressure (things turbochargers make plenty of), the fix until now has been to reduce the compression ratio of turbocharged engines. (The compression ratio is the ratio between the cylinder's maximum and minimum volumes, when the piston is at the bottom of its stroke versus the top). With direct injection, the spray of fuel during the compression stroke helps keep the cylinder cooler, reducing the possibility of knocking. This allows for higher compression ratios. That in and of itself can boost fuel efficiency by a few percent. When coupled with sophisticated electronic control of how much fuel to add with the turbo, the end result can be up to a 20 percent increase in fuel efficiency. That’s nothing to sniff at.
Here now
Sophisticated electronics and clever engineering have already had a significant impact on fuel economy in modern cars. Electronic control systems robust enough to last the tens or hundreds of thousands of miles of maintenance-free driving expected by today's car shoppers are now a reality. On their own, technologies like direct gasoline injection, electronic valve timing, variable displacement, and better forced induction each provide small but meaningful improvements in fuel economy. This is all happening right now, and the tech is already capable of saving you money at the gas station.
Join us next week for part two of this series, where we will take a look at future trends as carmakers gear up for even more radical changes in their bid to nearly double average fuel economy standards to 54.5 mpg by 2025.
No comments:
Post a Comment
Let us know your Thoughts and ideas!
Your comment will be deleted if you
Spam , Adv. Or use of bad language!
Try not to! And thank for visiting and for the comment
Keep visiting and spread and share our post !!
Sharing is a kind way of caring!! Thanks again!